本次鋼絲工藝生產是按照中鍍后拔的方法進行生產的,以外層鋼絲2.70mm鍍鋅鋼絲的生產流程為例,鍍層鋼絲的生產流程見圖2。
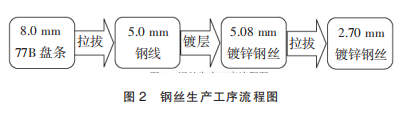
為增加公司產品的價格優勢,采用盤條直拔的方法進行生產,中間省去了盤條酸洗磷化和熱處理工序,降低了產品成本。鍍層采用Zn-5%Al鍍層,使鋼絲繩在3級鍍鋅級別的情況下依然具有良好的防腐性能。
從中間開始鍍鋅即可以保證鋼絲的鋅層級別,又可以保證鋼絲的韌性指標,緩解盤條直拔造成的韌性指標過低的現象。
2.2鋼絲繩捻制工藝
鋼絲繩捻制采用設備自帶的預變形器進行捻制,鋼絲繩的預變形和后調直根據現場的實際情況進行調整后,均可達到預期目標,如圖3、圖4為鋼絲繩在捻制時的預變形和后調直。
根據訂單要求,該鋼絲繩生產采用股涂油、繩不涂油的方式進行生產。在試生產剛開始時,鋼絲繩捻制沒有出現問題,隨著生產時間加長,鋼絲繩捻制出現了子繩鼓起的現象。
根據現場實際情況分析,出現這種情況的原因是鋼絲繩外股捻距大,子繩捻距小,隨著生產進行造成的子繩應力集中得不到有效的釋放造成的。當時提出的解決方案是調整子繩的翻身速率,更加有效釋放子繩應力,可以避免這種情況發生。逐步調整鋼絲繩子繩的翻身比之后,鋼絲繩子繩應力得到有效釋放,最終起鼓問題得到解決。
3問題與改進
3.1收線軸的設計
此次工藝生產是我公司第一次設計收線軸,內圓直徑與繩徑的倍數約為28.5倍,鋼絲繩沒有任何造成不能逆轉變形的跡象,在下次設計時可以相應地減小內圓直徑與繩徑的倍數,以節約生產成本和空間。
3.2鋼絲質量
由于采用盤條直拔的方式進行生產,所生產的鋼絲有部分鋼絲韌性指標不合格,約占總產量的5%左右。不合格鋼絲出現的沒有規律,可以通過優化盤條質量達到提高合格率的目的。
在拉拔過程中有局部鋅層脫落的現象。通過調整拉絲模角度,降低壓縮率等方法可以避免這種情況。另外,為了利于拉拔,在鍍完鍍層之后在鋼絲表面進行涂蠟處理,可以有效保護鍍層,利于鋼絲拉拔。
盤條從8.00mm拉拔至5.00mm,鋼絲平均強度為1590MPa,在鍍完之后鋼絲強度將為1510
MPa,鍍鋅過程鋼絲強度下降約80MPa。拉拔完成后,鋼絲強度范圍為1890~2044
MPa,可以達到1870MPa,可以在以后生產過程中酌情適當下調壓縮比,以提高韌性指標。在此工藝基礎上,我們生產出1870MPa級的鋼絲繩,鋅層質量145~178g/m2,大于船級社CCS為3級130g/m2的要求,且使用的是Zn-5%Al鍍層,防腐性能得到很大提高。
3.3鋼絲繩的捻制
鋼絲繩捻制除了要解決前文中提到的子繩起鼓問題之外,還必須調整好鋼絲繩的預變形器和后調直器,使鋼絲繩達到不松散的要求。6×37(b)類鋼絲繩,要求鋼絲繩切斷后股及股中鋼絲均不松散,可以適當減小股繩的捻距,使捻股后鋼絲產生的變形能減少,另外,捻股時適當加大鋼絲張力和壓線模的壓力,達到消除股中殘余應力的目的。在捻繩時,采用股預變形減少股繩中的殘存捻制應力,可以達到鋼絲繩不松散的目的。
在捻制時,需要隨著捻制的進行適當調整股張力。由于工字輪在捻制的不同時期重量存在很大差異,為了保證股的張力一致,必須在捻制一段時間后增加工字輪的阻尼帶張緊力,以保證捻制前后張力的一致性。股的長度盡可能的長,減少在后期股脫離工字輪后沒有了股張力造成的浪費,沒有股張力的情況下捻制的鋼絲繩應當做標記都判廢。